Rotational Molding
Rotomolding and intermediate bulk containers
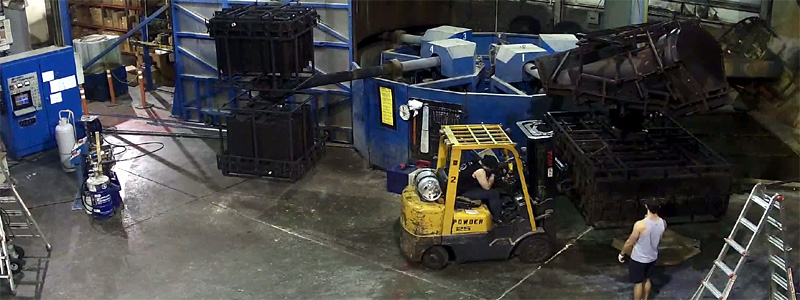
Rotomolding Intermediate Bulk Containers
The Rotational Molding process is utilized to manufacture a plethora of products ranging from nuclear waste tanks, playground equipment, air cargo containers, underground tornado shelters and the intermediate bulk containers. The rotomolding process starts by placing polymer materials that have been pulverized to powder into a mold that is heated while rotating bi-axially in an oven that is computer controlled for a determined length of time while continuing to rotate at a pre-determined speed. Once the cook cycle is complete, the arm moves into a pre-cooling station, where it continues to rotate while beginning to cool, either by means of ambient air, computer controlled fans or combinations of both. Once the pre-cool cycle is complete, the arm will move to a cooling chamber, where the mods are cooled by fans, water or a mixture of both for a pre-set amount of time in the cooling chamber. Once the cooling cycle is complete, the arm is brought out of the cooling chamber where the mold is opened up, the part removed and then the process starts all over again.

Because there are no required force or pressure involved, there is virtually no stress involved or molded into the products. This allows for products of the process to wildly durable. This durability is what allows for the IBCs to stand up to the rigors and abuses of industrial environments for decades on end.
The Intermediate Bulk Containers are rotationally molded and produced by custom rotomoldig leader, Granger Plastics Company. Providing high quality, rotationally moulded solutions for over 2 decades, Granger provides custom molded solutions for a variety of OEMS and manufacturers spanning a diverse range of industries. You can learn more about Granger Plastics at http://www.grangerplastics.com.
You can learn more about the rotomoulding process in the video below and check out http://www.rotationalmolding.com for additional rotomolding information.